5 Keys to Reducing Casting Defects Through Refractory Coatings
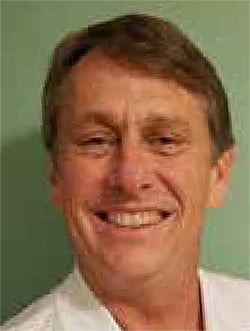
STANLEY FOREHAND | Fall 2020
Reprinted with permission from Simple Solutions That Work!
Download PDF: English
- Refractory Coatings are one of the products utilized to produce quality castings
- Controlled processes lead to better understanding of what is changing in foundries
- Learn the 5 keys to reducing casting defects through refractory coating
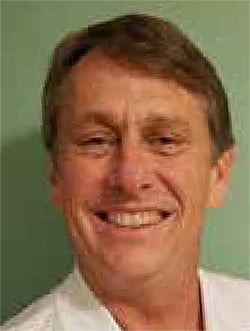
In an industry that has been around for many centuries with a wealth of knowledge and experience, we still today find ourselves when analyzing casting defects asking, “what changed?†This is because we understand that our industry is process dependent and controlling those processes is key to success. Refractory coatings are one of the products that we utilize to produce quality castings. Although usage is small in comparison, these products are applied at the mold/metal interface which is critical when it comes to defects. Crushes, inclusions, scabs, expansion, gas, metal penetration, misruns and rough surface defects can all be affected by refractory coating practices. Therefore, how do we control this aspect of our foundry operations?
Typical Refractories Utilized
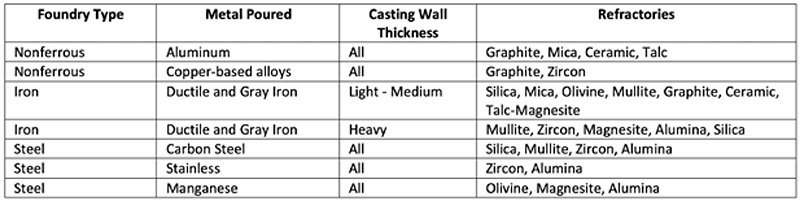
5 KEYS TO REDUCING CASTING DEFECTS THROUGH REFRACTORY COATINGS
- Selection of Coating
- Coating Preparation
- Quality Control
- Proper Application Techniques
- Proper Drying of Coating Deposit
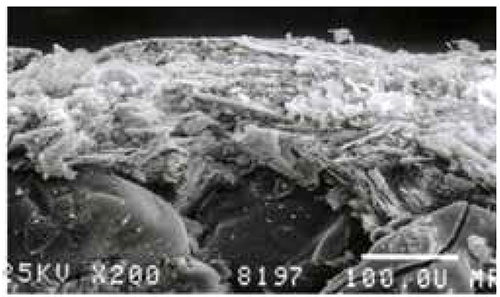
Microscopic View of Applied Refractory Coating
KEY #1: SELECTION OF COATING
Choose the right refractory blend for your application. A refractory coating is a protective material, applied to a core or mold surface, to enhance the surface finish of the casting and reduce defects that occur at the sand-metal interface. They accomplish this by filling voids, increasing the refractoriness of the mold or core, improving sand peel, and controlling what is happening in the mold. The refractory component is the workhorse of the coating. Coating suppliers utilize a wide range of refractories and can customize a coating to your foundries needs. Open conversation with your supplier is key to getting the right coating for the job.
KEY #2: COATING PREPARATION
We must understand a fundamental truth that a coating is only as good as the core or mold surface upon which it is applied. The goal is still to get the right amount of properly prepared coating on the core or mold every time. Coatings contain multiple components and are slurries, not solutions. They typically are shipped as a heavy slurry to avoid settling and shipping a large carrier component. These factors make mixing until homogenized very critical to the process. Suppliers have formulized steps to help in this area, but the foundry must still do their part to insure a well-mixed, homogeneous product is being used in production.
- Utilize the right size mixer to get good mixing without shearing.
- Assure movement without dead spots while avoiding air entrapment or vortex.
- Choose the proper blade and proper rotation to move the coating around and across dip tanks.
- Coating tank design is also critical. Stainless steel construction, round or rounded corners, baffles, 2:1 to 3:1 tank to blade diameter, and mixer off set and placement are key.
- Document the coating preparation process.
Whatever type of mixing and tank design your foundry has decided on utilizing, make sure the coating is well mixed before placing into service and then properly mixed while being used. This is a major source of coating variation in the foundries of today.
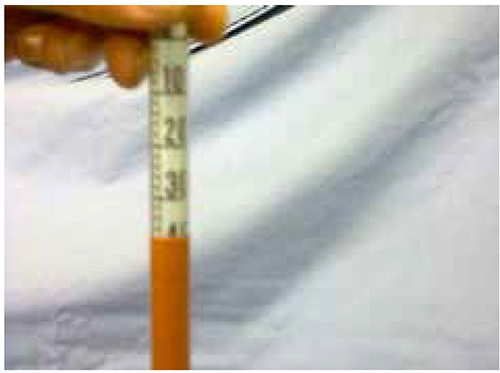
Figure 1: Baume
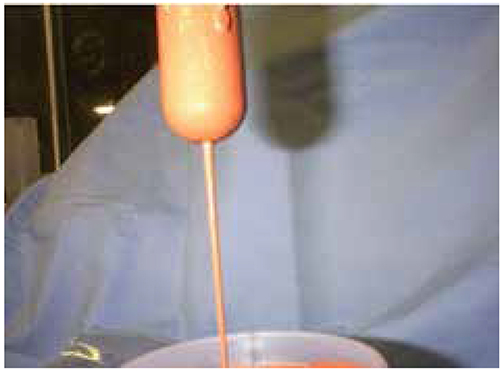
Figure 2: Flow Cup
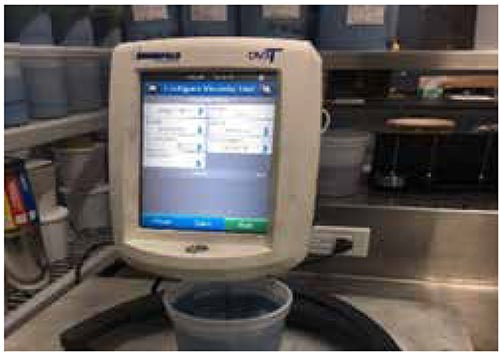
Figure 3: Brookfield Viscosity
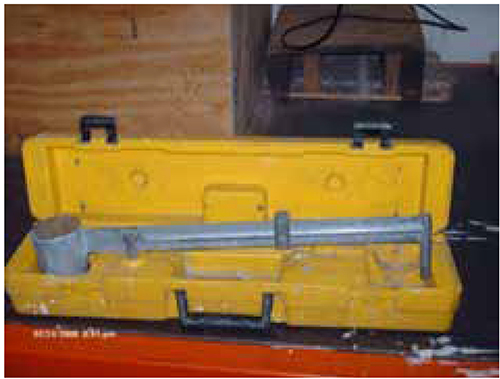
Figure 4: Density (weight per gallon)
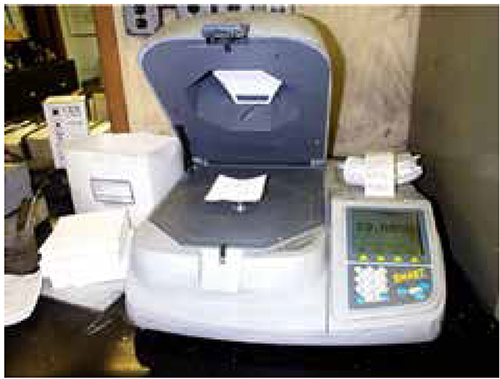
Figure 5: % Solids
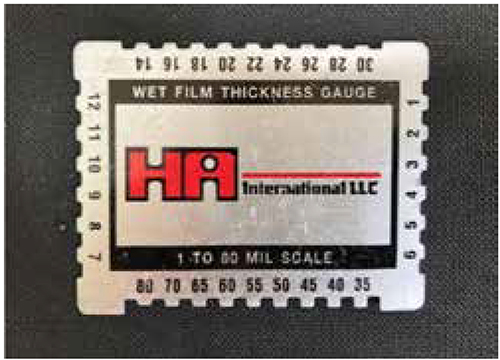
Figure 6: Wet Mil Thickness
KEY #3: QUALITY CONTROL.
Once the coating is mixed and diluted to the operating parameters, it must be controlled. There are several test methods available to the foundry and new technology is being developed around those methods every day. We are seeing more automation and real time testing that take out some of the operator variation but the fundamental tests are the same. You should incorporate at least 3 of the following into your control plan. Foundries are multivariable so our test methods have to be multivariable if we want to get a true picture of what is changing. Checking multiple properties of the coating is key.
- Baume - Figure 1
- Flow Cup - Figure 2
- Brookfield Viscosity
- Density (weight per gallon)
- % Solids
- Wet or Dry Mil Deposit Thickness
KEY #4: PROPER APPLICATION
Technique. Remember the goal is to get the right amount of properly prepared coating on the core or mold every time. Whether you are dipping, spraying, brushing or flow coating, it is important to minimize variation in technique. Concentrate on several key parameters for each method. All of the following process parameters can impact coating deposit, coating penetration and the resultant barrier layer that is established at the mold metal interface.
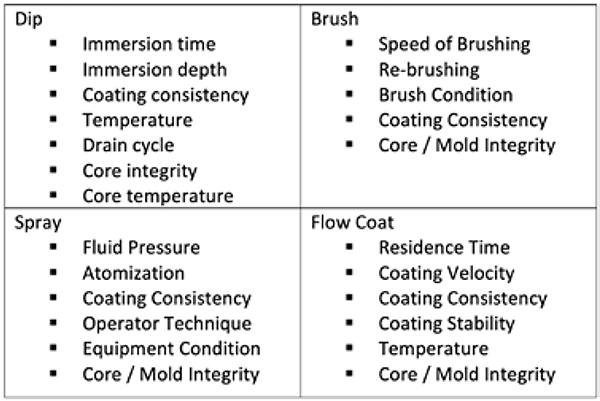
Key Application Process Parameters
Many foundries have incorporated robotic dipping into the process where the casting mix will allow it. Operator training is critical where robotics are not possible. The elimination of tear drops, runs and drips, and heavy coating deposits will reduce the resulting casting defects associated with these issues. Baume, viscosity, and mixing controls are essential. Prevention measure should also be in place to minimize sand contamination in the coating dip tanks. This will result in sand inclusion defects and rough surfaces on the castings.
The spray process presents different challenges. Properly adjusted spray equipment will help control the deposit on the core or mold surface. Most operators will adjust the equipment to their touch but the deposit must stay the same. Over atomization of the coating, too low a pump pressure, and spray distance can all have adverse effects on performance. In this application you are relying on the gun pressure, gun distance and coating consistency (Baume) to work the coating into the surface and form the desired barrier. Standardizing these factors is crucial to consistent casting results.
Two of the main issues associated with brush application are inconsistent coating thickness and brush marks. Inconsistent coating thickness can result in potential metal penetration, erosion, and gas defects. Brush marks can result in poor surface finish and rough surfaces on the casting. Using a good quality brush or swab with proper viscosity coating will fix these issues. Also avoid re-brushing an area after the initial coat has matted but not completely dried.
The final application method is flow coating. Just like in the previous applications, coating consistency and properties are important and will control how the coating flows over the core or mold surface. It is important to create a smooth flow from the wand tip. Coat from top to bottom and move at such a pace to get a good consistent deposit in one pass. If you have to go back over missed areas the deposit across the face you are coating will not be consistent. This can cause multiple casting issues at the mold metal interface: penetration, surface finish, core set issues, heat transfer and others. Sand contamination in catch basins is also an issue with this application technique resulting in inclusion type defects.
Many variables can affect the application. Regardless of application type, best practice is to document the standard process for coating application. A standardized process with ensure consistent performance of your coating.
KEY #5: PROPER DRYING OF COATING DEPOSIT
All coatings have a carrier component that is designed to get the refractory component onto the surface and in between the sand gains. Once this is accomplished, the water or solvent carrier must be removed from the process by some type of drying method. There are time, temperature, and air movement components to this process and all are equally important. Drying oven temperatures must be controlled along with air flow through the ovens. Dwell time in the ovens adequate to remove all the water is a must. Timing of light off is important when using alcohol coatings. Lighting off too early can result in blistering and poor casting finish. Lighting off too late can result in residual alcohol left in the core/mold or too deep of coating penetration. Do not just assume that dry is dry and how you get there is not important.
SUMMARY
Refractory Coatings are one of the products that we utilize to produce quality castings. We do that by getting the right amount of properly prepared coating on the core or mold every time. Following these 5 keys will help us accomplish that task.
- Selection of Coating
- Coating Preparation
- Quality Control
- Proper Application Techniques
- Proper Drying of Coating Deposit
Better controlled processes lead to better understanding of what is changing in our foundries. Partnering with a quality coating supplier with open communication about issues will also be beneficial.
This enables us to work together to address issues with sound judgement, factual data and proven methods to correct the casting defects as they arise - and they will! Control your process - don't let it control you.