Aluminum Fluxes 101 - Basics of Furnace Cleaning, Dross Handling and Wall Cleaning
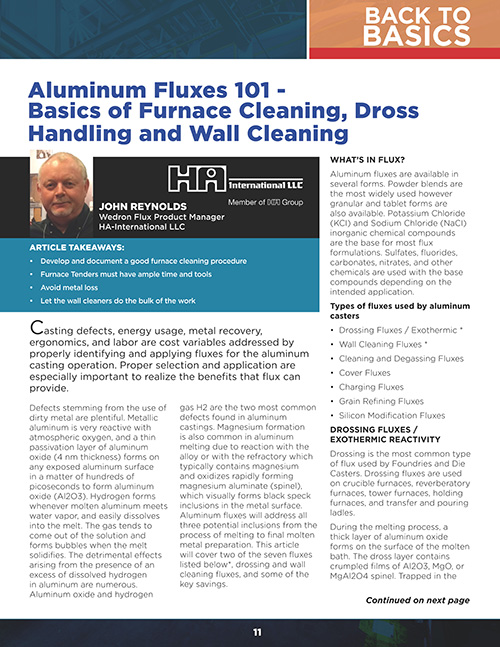
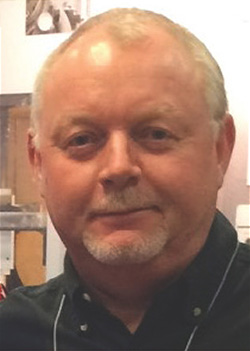
JOHN REYNOLDS | Fall 2022
Reprinted with permission from Simple Solutions That Work!
Download PDF: English
- Develop and document a good furnace cleaning procedure
- Furnace Tenders must have ample time and tools
- Avoid metal loss
- Let the wall cleaners do the bulk of the work
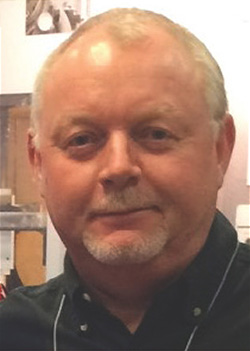
Casting defects, energy usage, metal recovery, ergonomics, and labor are cost variables addressed by properly identifying and applying fluxes for the aluminum casting operation. Proper selection and application are especially important to realize the benefits that flux can provide.
Defects stemming from the use of dirty metal are plentiful. Metallic aluminum is very reactive with atmospheric oxygen, and a thin passivation layer of aluminum oxide (4 nm thickness) forms on any exposed aluminum surface in a matter of hundreds of picoseconds to form aluminum oxide (Al2O3). Hydrogen forms whenever molten aluminum meets water vapor, and easily dissolves into the melt. The gas tends to come out of the solution and forms bubbles when the melt solidifies. The detrimental effects arising from the presence of an excess of dissolved hydrogen in aluminum are numerous. Aluminum oxide and hydrogen gas H2 are the two most common defects found in aluminum castings. Magnesium formation is also common in aluminum melting due to reaction with the alloy or with the refractory which typically contains magnesium and oxidizes rapidly forming magnesium aluminate (spinel), which visually forms black speck inclusions in the metal surface. Aluminum fluxes will address all three potential inclusions from the process of melting to final molten metal preparation. This article will cover two of the seven fluxes listed below*, drossing and wall cleaning fluxes, and some of the key savings.
WHAT’S IN FLUX?
Aluminum fluxes are available in several forms. Powder blends are the most widely used however granular and tablet forms are also available. Potassium Chloride (KCI) and Sodium Chloride (NaCI) inorganic chemical compounds are the base for most flux formulations. Sulfates, fluorides, carbonates, nitrates, and other chemicals are used with the base compounds depending on the intended application.
Types of fluxes used by aluminum casters
- Drossing Fluxes / Exothermic *
- Wall Cleaning Fluxes *
- Cleaning and Degassing Fluxes
- Cover Fluxes
- Charging Fluxes
- Grain Refining Fluxes
- Silicon Modification Fluxes
DROSSING FLUXES / EXOTHERMIC REACTIVITY
Drossing is the most common type of flux used by Foundries and Die Casters. Drossing fluxes are used on crucible furnaces, reverberatory furnaces, tower furnaces, holding furnaces, and transfer and pouring ladles.
During the melting process, a thick layer of aluminum oxide forms on the surface of the molten bath. The dross layer contains crumpled films of Al2O3, MgO, or MgAl2O4 spinel. Trapped in the films are droplets of non-oxidized aluminum. Flux is applied to the dross layer and mixed in using a rake or skimmer. The flux reacts to create thermite and generates heat, promoting coalescence of the Al droplets and flow back into the aluminum bath. Thermite is a reaction between the flux, available oxygen, and aluminum. When ignited or heated, it gives off an enormous amount of heat as a result of the chemical combination of the aluminum with the oxygen of the oxide. The reaction temperature is estimated to be about 2,400° C (4,400° F). If cleaning a reverberatory furnace the thermite will soften oxide buildup on refractory walls at the metal line and removes the metal from the oxide to facilitate easy separation for the aluminum to drop into the melt. A rake or scraper should be used to remove the oxide.
DROSSING FLUXES / ALUMINUM RECOVERY
The most economical aspect recognized by a caster is metal recovery. When properly used, a good drossing flux can reduce the metallic content in the dross by over 50%. If no flux is used the dross is considered wet as shown in figure 1. The proper flux addition will result in a dry dross. Excessive flux addition will lead to metal loss. A small percentage of aluminum is consumed by the exothermic reaction.
In figure 2, the dross has a light gray appearance with some thermite. This dross should be allowed to cool before placing into a dross hopper. If excessive thermite occurs while following the documented process, a review should take place and any changes documented.
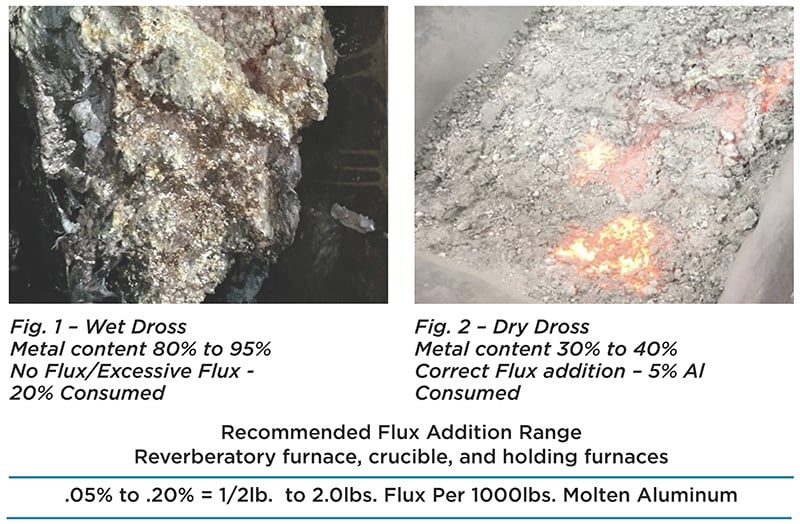
EXCESSIVE THERMITE
Excessive thermite will consume aluminum in the furnace and dross pan. Dross will glow white hot and generate fumes when agitated, once cooled a white powder dross will be evident and virtually all recoverable metal consumed.
COOLING / EXTINGUISHING THERMITE
- Appropriate Personal Protective Equipment (PPE) is required while handling dross.
- Keep dross away from air movement, fans, open doors, or windows.
- Spread the dross over a large area, this will allow the thermite to cool quickly.
- Hot thermite dross should not be mixed with other dross containing a high percentage of aluminum.
- Cover the thermite dross with a layer of dry rock salt, thus smothering the thermite.
- Reclaim dross pans can remove molten aluminum and reduce thermite.
- Incorrect flux selection or excessive flux addition are the two most common causes of excessive thermite.
DROSSING FLUXES / GAS FIRED REVERB FURNACE CLEANING
Flux addition rates will vary depending on how often the furnace is cleaned, charge material, and throughput. When developing a cleaning procedure for any furnace, it's best to start on the low end of the flux addition range and increase as needed to achieve desired results. Multiple cleanings will be required to zero in on the addition that works best for the furnace. Once again, develop, document, and follow the procedure. Weighing the dross and a visual inspection after each cleaning is a common practice during the procedure development.
Furnace cleaning is a physically demanding task, even more so for large reverb furnaces. Furnace tenders must be given adequate time, proper tools in good condition, PPE, and training to perform the task. The furnace in figure 3 is a 20,000 lb. gasfired reverb and had a complete refractory reline 14 months before the photo date. If properly cleaned using a good flux and procedure, the lining should have a life span of 4-7 years. This furnace was not properly cleaned and needed to be shut down for rebuild after 16 months in service. Tear out was very difficult and expensive due to the extensive corundum.
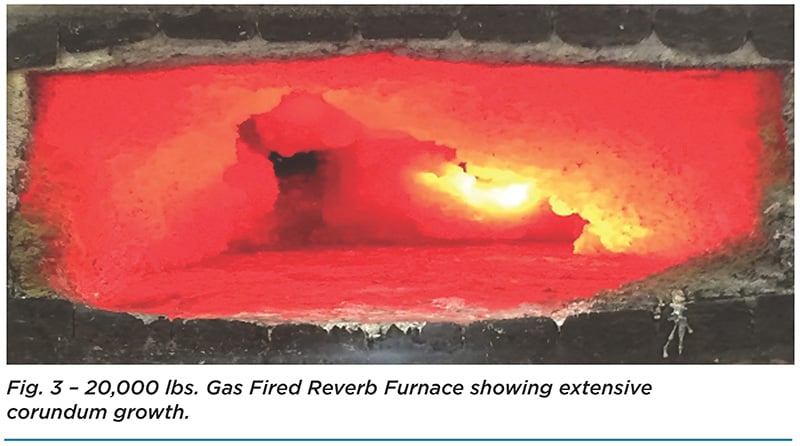
WALL CLEANING FLUX
These fluxes are either sodium-free or sodium-bearing. Alloy chemistry should always be reviewed before selecting which will work best for the application. A refractory lining will have a service life of 4-7 years if properly maintained. Over time the lining loses its nonwetting ability allowing aluminum and oxide to adhere to it. This commonly occurs at the metal line in a reverb furnace. Oxide growth is also affected by air infiltration, burner calibration, and furnace design. Once it’s determined that regular cleaning is not effectively removing the buildup then a wall flux should be used. Wall fluxes contain high percentages of oxidizers and fluorides and should be used as directed.
APPLICATION PROCEDURE
- This procedure should be done just prior to a general scheduled cleaning.
- Apply the wall flux only to buildup areas. If needed, a pneumatic flux gun can be used in larger furnaces.
- For best adherence, areas to be treated should be red hot.
- Once applied, close the furnace door, and run up to the high fire for 10-15 minutes.
- Drive to low fire and open the door. Using an appropriate tool, scrape areas treated.
- After scraping the walls, a general scheduled cleaning can be done.
Again, furnace cleaning is physically demanding. Furnace tenders often aggressively scrape, and chisel build-up areas after a wall flux has been applied and see very little progress. This can be discouraging and lead to discontinuing the use of the wall flux. Corundum Al2O3 takes time to get under control and is never completely removed, only kept at bay. When scraping corundum after a wall flux is applied, effort is required, but don’t overdo it.
Apply before each scheduled cleaning and scrape each time. Assuming the corundum has penetrated the refractory, it's best to leave a thin layer of the oxide on the wall. Removing all the growth can result in refractory damage. Over time, the buildup will be reduced, and the use of wall flux suspended. Resume applying the wall flux when needed, a good well-trained furnace tender can make this call. Supervision should make weekly visual inspections to confirm the furnaces are cleaned correctly.
Proper flux selection and good process quality control are especially important to realize the benefits in eliminating casting defects and reducing energy usage while increasing metal recovery. Applied with good process control, improved worker ergonomics, and gains in labor utilization are also key variables that are directly impacted.