Optimized Feeding Systems
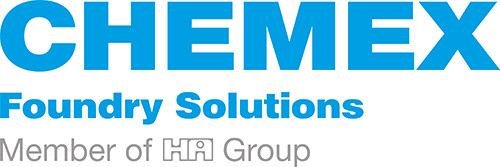
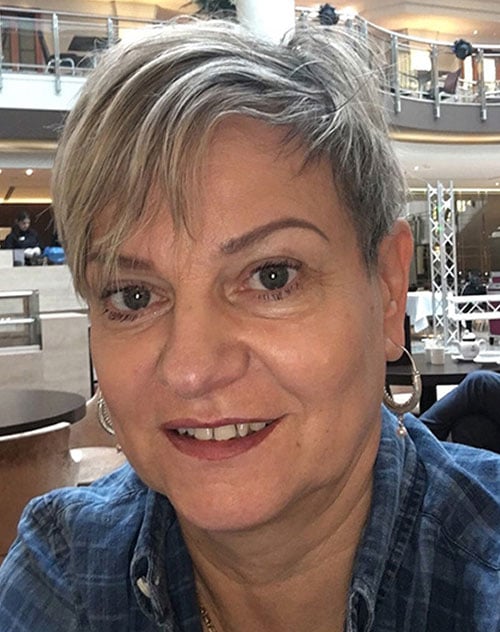
SVETLANA DODIK-PELJA | Spring 2019
Reprinted with permission from Simple Solutions That Work!
Download PDF: English
- Exothermic sleeves for demanding casting designs
- Compact feeders for liquid metal savings
- High strength cold box feeder systems for automatic sand molding, eliminates sand around contact and feeder breakage
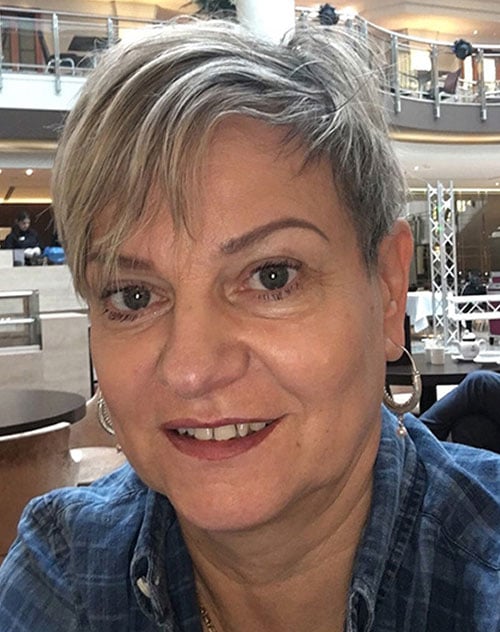
It is well known that metals change volume during solidification. This volume change must be compensated during solidification otherwise shrinkage defects can occur in a casting, making it unusable for its stated purpose.
This has been solved through the use of adding a metal reservoir commonly known as a "feeder" the purpose of which is to supply liquid metal to the casting as it cools and solidifies.
As this technology has developed and been improved, newer types of feeder materials have become available, including combinations of exothermic-insulating and highly exothermic compositions. The choice of material depends upon the application.
For more demanding casting designs, highly exothermic sleeves have become more wide-spread. The exothermic reaction is started when molten metal meets the feeder. This initiates a highly energetic reaction generating heat. This keeps the metal, contained within the feeder, liquid and extends the feeder solidification time to a greater degree than insulating feeders. The benefit has been to minimize feeder volumes and improve casting yields.
To take advantage of these new opportunities, compact feeder designs using sodium silicate binder systems with glued-on breaker cores (typically made using resin coated sand) were used and still are today. Due to their much lower volume, this yielded savings in liquid metal and gave better productivity to the molding line.
Even with this system, reduced breaker core diameters of the compact feeder systems and the use of pins mounted directly on the pattern, resulted in increased possibilities for locating the feeders on the casting.
Subsequent development of faster green sand molding equipment with increasingly higher compressive pressure to produce castings with tighter tolerances, has created requirements for more feeder sizes and different geometries to feed complex and thin-walled castings. However, the higher compressive pressures of modern molding machines, which result in higher hardness of the green sand needed to produce near net shape castings, result in frequent damage to the breaker cores and feeders
The introduction of cold-box (c-b) bonded feeding systems solved this problem by providing a feeder with high strength to resist the compressive force of today's molding machines, yet allow complete collapsibility and burn-out during the casting process. In addition, c-b bonded feeders exhibit repeatable, precise tolerances, and can be shipped long distances without damage and stored for long periods of time without degrading.
Newer designs, with compressible lower parts, such as the telefeeder, offer unique advantages during use. During compaction of the green sand, the upper section of the tele-feeder slides telescopically over the lower section. This means that the lower section is not exposed to the molding pressure and, therefore, damage.
When the upper section slides over the lower section, additional compaction of the green sand under the lower section takes place. This is the transition area between feeder and casting, precisely where poorly compacted sand may occur with other designs.
Tele-feeder designs using exothermic materials in both upper and lower sections guarantees that such feeder designs provide up to 50% efficiency rate of their volume to the casting. And the introduction of very low-to-no fluorine exothermic materials used in c-b feeders provides on-going benefit for the recirculating green sand system.
The valuable benefits in practice has been the formation of a defined break-off point as a part of contact area that enhances separation of the feeder from the casting and significantly reduces cleaning costs compared to other designs.
The most powerful value of the tele-feeder is the exothermic neck which allows:
- The connection between the casting and upper part of the feeder stays hot for a longer time, without increasing feeder size.
- The neck geometry provides directional solidification and avoids undesirable matrix degeneration around the contact area.
- The significantly reduced contact area of the tele-feeder allows for many options in positioning the feeder on the casting to provide very accurate feeding of critical spots on the casting prone to shrinkage.
Further benefits include:
- The centering pins have a very simple maintenance-free design and are relatively inexpensive to manufacture.
- The centering pins provide an air vent during the molding process.
All these benefits enhanced reasons to use the tele-feeder technology to make shrink-free castings with significant savings in molten metal and reduced or eliminated time in the cleaning operation.
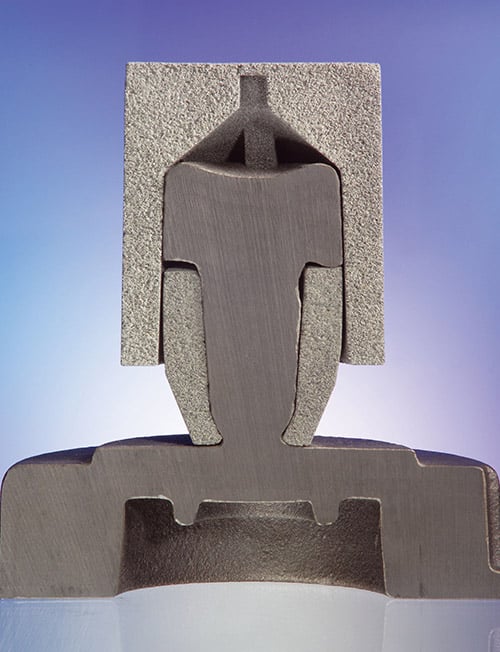
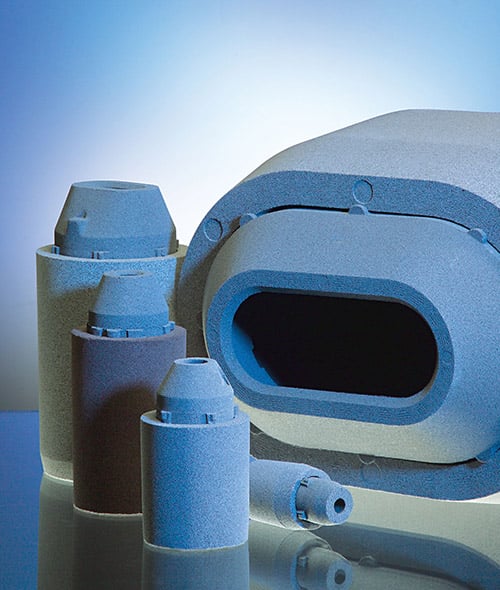