How does Additive Manufacturing work in practice?
Across the foundry industry, additive manufacturing enables foundries to produce prototypes and very limited series without high tooling and storage costs. Additive manufacturing also gives designers unprecedented freedom in the design of molds and cores.
A molding material (e.g. silica or ceramic sand) containing a binding agent is deposited in micrometer-fine layers onto a build platform. A printer head then selectively doses the layer with a powder or liquid activator. The printing solution discharged via the print head triggers the curing process that causes the molding material particles to fuse together. This process is continued layer by layer until the desired shape is produced.
After printing, the molds and cores are freed from the surrounding unbound molding material.
Depending on the system, unprinted molding material can be returned to the process in whole or in part after further processing. Depending on the binder system and strength requirements, the cores and molds are placed in an oven for a few hours after the layering process to dry them out and get them ready for casting. To improve their casting properties, the cores, and molds can be coated with one of HA’s specially developed coatings.
.jpg?width=1622&height=599&name=3d_printer_head%20(1).jpg)
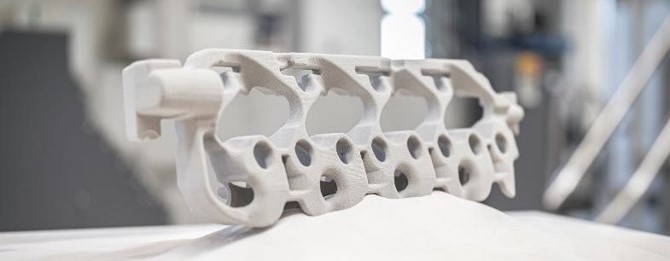
Products for binder-jetting
HA-International has been pioneering additive manufacturing within the foundry industry since the dawn of the “3D printing age”. We offer a range of binder systems precisely tailored to all major printing systems.Special emphasis is placed on the development of inorganic binder systems. Environmentally friendly 3D printing is thus no more and no less than the next logical step towards an environmentally compatible end-to-end production process.
At the same time, we also feel obligated to further optimize our existing, tried-and-tested processes to more carefully steward natural resources and protect the environment.
3D printing with inorganic binder systems
With our inorganic binder systems for series production, 3D printing aligns with the accelerating trend towards environmentally friendly molding materials in the foundry.
Unlike organic systems, inorganic binders do not burn during the casting process and therefore do not produce smoke, odor, or other environmentally harmful emissions. In order to speed up the reaction process, the build chamber is usually heated using infrared panels or bulbs.
Once the printing process has been concluded, the cores and molds are then additionally cured in a microwave oven until their final strength is reached.
- 100% inorganic binder
- High resolution
- Diverse application possibilities
- Good strength properties immediately after printing
- No emissions
- Good decoring ability
Resource Saving Printing with Furan Resin
Our Enviroset 3D Resin allows for the use of both 3D printers with separate mixing systems, usually referred to as the dry-mixing process, and printers with integrated mixing systems.
We have developed qualified activators for both systems and matched them to our binder systems. Owing to the stable storage properties of the activator and sand mixture, the mixing process can be decoupled from the sensitive printing process. The printed cores and molds cure by themselves.
At least 30% of the activated unprinted sand can be reused, and there is no need for post-curing in an oven.
Advantages of 3D sand printing with furan resin
- Diverse application possibilities
- Good strength properties right after printing
- Applicable for most alloys
- Inexpensive materials
- No post-treatment necessary
- Self-curing
- Perfect decoring
3D printing with phenolic resin
As an alternative to 3D printing with furan resins, we also have a range of phenolic resins specially developed for the additive manufacturing 3D printing process. They feature excellent mechanical strength, extreme dimensional stability, exceptional contour sharpness, and high thermal resilience.
Our phenolic binder systems make it possible to print complicated geometries and undercuts that would otherwise be very difficult or even impossible to produce.
The sand is not activated prior to printing as described above but is added as raw sand. Infrared lamps are integrated into the printing process to speed up the curing process. All of the unprinted sand can be collected and reused. This leads to excellent de-sanding properties in the finishing process.
Advantages of 3D printing with phenolic resin
- Versatile applications
- Maximum accuracy and dimensional stability
- Outstanding surface quality
- High thermal resistance
Coatings for 3D printing
Foundries that use 3D printing for their molds and cores can rely on products specifically developed for the process. The use of coatings specially developed for 3D printing can prevent the formation of rough casting surfaces and sand adhesion.
The strengths of coatings for 3D printing
- For application in iron, steel, and aluminium casting
- Avoidance of casting defects
- Smooth surfaces
- Application properties tailored to different printing processes
For additional product information, contact Kelley Kerns, Director - New Business Development at 630-575-5734 or Kelley.Kerns@HA-Group.com