High-Quality Resin Coated Sands for Shell Molding and Superior Metal Casting
The shell molding process was originally developed by the German inventor Johannes Croning and has been reliably used in foundries around the world for more than 75 years. Even today, shell molding is indispensable in the production of certain cast components, especially as it is so easy and delivers such high-precision castings.
About the shell molding process
With the invention of the shell molding process, Johannes Croning developed a new, stand-alone mold casting process based on an entirely new production principle, as well as an innovative resin-bonded molding material for the production of castings. The biggest difference between this process, for which a patent application was filed in 1944, and the compact, box-bound mold casting processes was the shell- or mask-like reproduction of the outer contour of the casting mold, which is what gave the process its name.
Today, shell molding is a technically mature, extensively tested production process for shell and core manufacturing. With regard to the dimensional accuracy of the resulting castings, the shell molding process is still the most accurate sand-casting process in the foundry industry.
HA offers foundries that use the shell molding process, a wide range of coating resins, finished sands, and finished molding materials.
Information on our production facility
May 10th, 2024, marks 50 years of operations out of our Oregon, IL, Resin Coated Sand facility. Our plant is supported by three fully automated production lines and analytical data tracking to ensure every batch meets your required specifications. With a wide array of resins, silica & non-silica aggregates, and additives, we are well-equipped to provide solutions for even your toughest challenges.
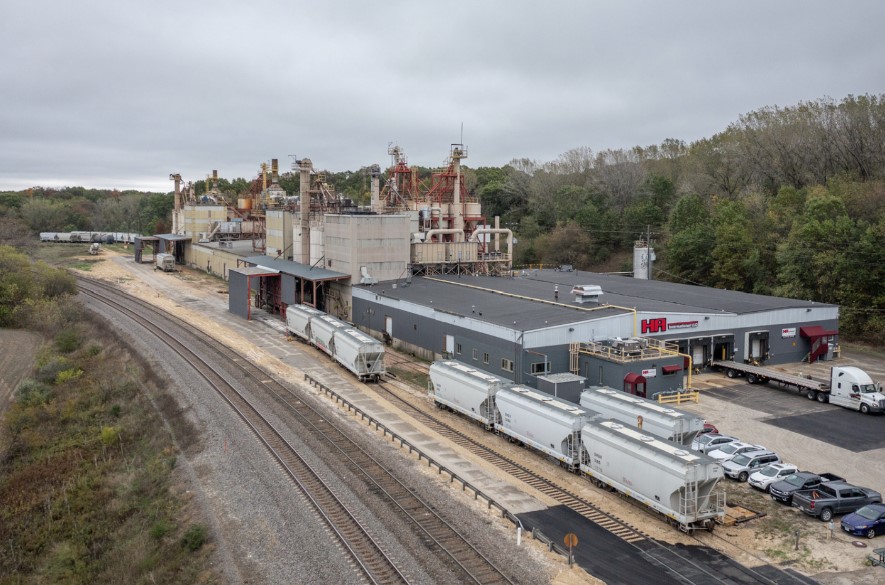
HA Custom Coated Sands
With a wide array of resins, aggregates, and additives to select from, HA's Custom Coated Sands are tailored to meet the performance expectations of your unique process.
- A faster build-up of sand helping reduce invest times
- Good cure through and uniformity of cure
- Excellent sand flowability with high resistance to peel back
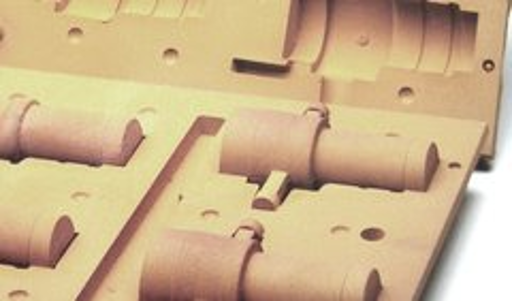
EcoMission Designation 
Minimizing our impact on the environment is part of HA's EcoMission. To be recognized as an EcoMission classification, each of our products must meet at least three out of five environmental criteria.
- Utilizes water or renewable components - Water-based components used for manufacture.
- Utilizes recycled components - Recycled phenol is used for resin manufacture to reduce waste generation, and recycled sand is used when available.
- Low Volatile Organic Compound (VOC) - Lowest free phenol resins available are used to minimize VOC emissions in the coating operation and in the resin coated sand.
- Low Hazardous Air Pollutant (HAP) - Lower formaldehyde levels generated at core and mold making and low free phenol contents reduce the HAPs generated during use.
- Low Odor -Formulated with a new deodorizer, along with low nitrogen levels and low free phenol levels, resulting in noticeably lower smoke and odor in the core shop.
EcoFlo 3.0 
EcoFlo 3.0 is the next generation of environmental series resin coated sand that is part of the HA International EcoMission product line. It is designed to maintain low ammonia and formaldehyde emissions while having increased strength compared to other environmental grades. This allows for the potential to reduce the total resin content required for environmental resin coated sands or the ability to maintain resin levels of conventional grades if converting to environmental.
Advantages
- Reduced Emissions – 70% reduction in ammonia and formaldehyde emissions when compared to conventional formulas.
- High Humidity Resistance – Increased humidity resistance is substantial, especially when compared to other environmental grades of resin coated sand.
- Low Lumping – Reduced lumping means better flowability in hot and humid climates, which also reduces the need for additional processing.
- Increased Strength – Increase in tensile strength when compared to other environmental grades.
Benefits
- Drop-in replacement for the incumbent grade at a lower resin content
- Higher sand tonnage allowance within the same VOC permit tier
- Lower core-making emissions for an improved operator environment
- Potential to improve cycle times during core-making
- 6-14% Reductions observed on specific jobs
Custom Coat
Our Custom Coat product line is designed for today's demanding foundry applications. This sand has been designed to provide high levels of productivity by using the latest technology available to the foundry industry.
Our Custom Coat products are produced and manufactured to your product's exact specifications:
- Resin content: 1-5%
- Hexa content: 10%+ (BOR)
Custom Coat E-Series 
Our resin coated sand product line includes Custom Coat E-Series, an environmentally compliant line of formulas that reduces ammonia and formaldehyde emissions by 30% and 60% from conventional formulas. Our Custom Coat E-Series formula incorporates all odor-reducing methods:
- Resin content: 1-5%
- Hexa content: 5% maximum (BOR)
- Liquid resin curing agent included
- Low odor
Custom Coat EcoFlo 
CC EcoFlo is an environmental resin coated sand that is part of the HA EcoMIssion product line. CC EcoFlo is designed to reduce both ammonia and formaldehyde emissions while improving humidity resistance compared to other environmental grades. CC EcoFlo maintains strength in shell cores, emits minimal ammonia, and, most importantly, reduces lumping propensity, even in hot and humid conditions.
Advantages:
- Reduced Emissions
70% reduction in ammonia and formaldehyde emissions when compared to conventional formulas - Increased Humidity Resistance
Increased humidity resistance is substantial, especially when compared to other environmental grades of resin coated sand - Reduced Lumping
Reduced lumping means better flowability in hot and humid climates, which also reduces the need for additional processing
Troubleshooting the Shell Process
Operating problems can occasionally crop up, even in the most carefully supervised shell process operations. When they do, quick corrective action can make the difference between a minor inconvenience and a serious dollar expense to the foundry.
Our troubleshooting poster draws on the experience of HAI’s field and laboratory personnel to summarize some of the more common shell process operating problems with suggested solutions that have been successfully used in foundries.
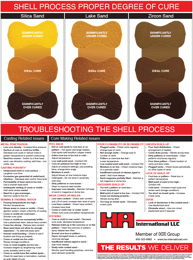
Your contact
Sam Christensen
Product Manager Resin Coated Sand & Specialty Aggregates
.png?width=350&height=350&name=Untitled%20design%20(39).png)