Versatile Refractory Coatings for Diverse Foundry Applications
The term coating refers to the techniques used to smooth the surface of manufactured parts. In foundry technology, coatings are substances that are applied to molds and cores to smooth the porous surface of the molded part. Finely ground refractory to high-refractory materials are used as a base material. The coating layer insulates the substrate and protects against thermal stress from the molten metal.
Immaculate casting surfaces More efficient process Prevention of defects Controllable properties
As one of the most important suppliers of foundry chemical products worldwide, HA Group offers coatings for all applications in automotive, hand mold, and other casting processes.
As a result of the constant advances in binder system technology, coatings are also constantly adapted to ever-changing requirements. This is made possible by using new raw materials tested and adapted during continuous research and development work.
We can also meet the continuously increasing demand for water-based coatings with a broad product range.
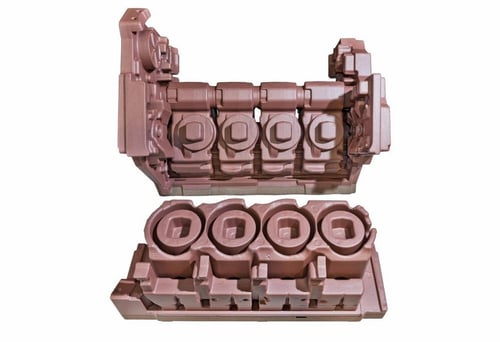
Strengths of HA Coatings
Excellent casting surfaces can only be achieved with the right coating. Typical casting defects such as veining can be avoided, and reworking and the associated costs can be significantly reduced.
HAI’s comprehensive product portfolio includes coatings for all applications, application types, and storage conditions.
- Surface with the latest technology
- Uniform coating structure
- Stable workability
- Controlled rheological properties
- Improved temperature stability of the molding material
- Avoidance of casting defects such as penetration or veining
- Controlled gas permeability
- Minimal reworking
- Alcohol and water-based coatings for all requirements
- Optimized application through cooperation with manufacturers of application and processing equipment
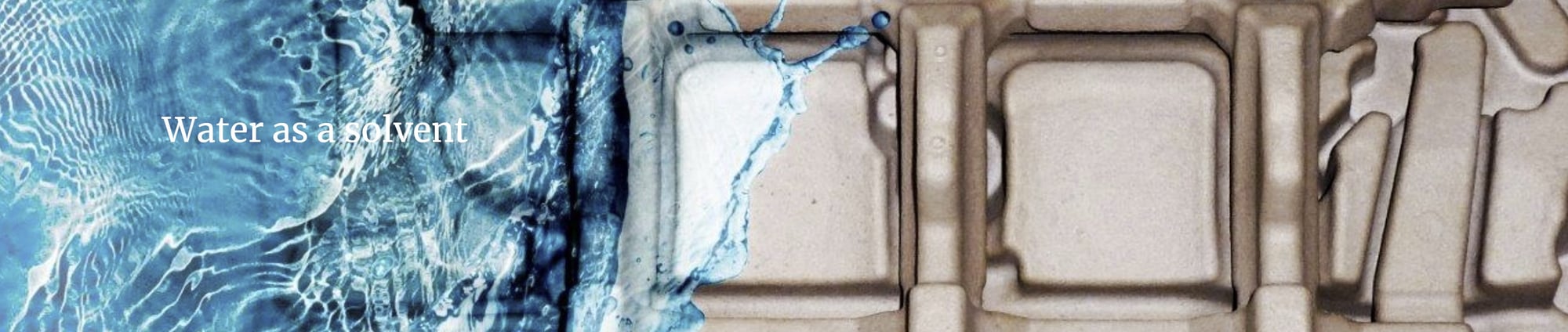
Continuous further development
What were once simple coatings have now become complex multi-component systems for a wide range of applications. By making fine adjustments to the composition of the refractory materials, carrier liquid, binders, and other input materials, our coatings can be adapted to all specific conditions.
In addition to delivering the best technology at the best prices, we also strive to maximize the sustainability of our products – both in production and in use in the foundries.
The changeover from alcohol-based to water-based coatings has persuaded many customers to opt for this emission-free, cost-effective, and storage-stable solution – with excellent casting results. The same goes for conventional coatings, where our research focuses on reducing emissions and conserving resources.
In our laboratory in Westmont, a dedicated team of experts is committed to the new and further development of coating systems.
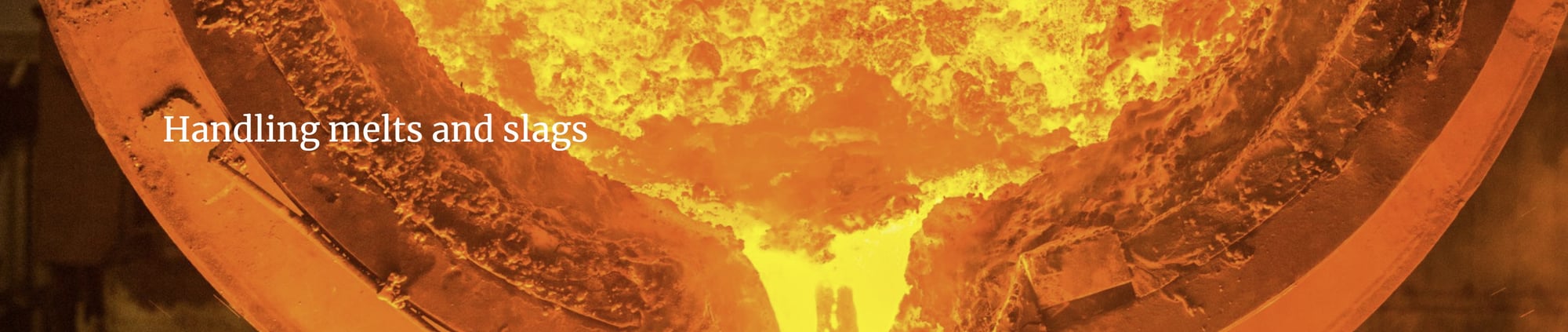
New refractory coatings
Wherever metals are melted and further processed, operators of furnace plants and slag management employees work against the resulting contamination of the respective refractory materials and metallic surfaces. In some cases, a considerable amount of time is required to remove the solidified material from the respective areas. In addition, any damage that may occur must often be repaired in a time-consuming process.
Reducing the cleaning effort
HA International coatings can withstand various applications involving melts and slag. Due to intensive research and development, our customers can rely on our products to provide an abrasion-resistant protective film that is thermally stable after complete drying. The coating has an optimum influence on the wetting angle and prevents adhesion.
After dilution of the pasty raw products, the respective coatings are applied by spraying, brushing, or dipping, effectively preventing the accumulation of melt residues. This applies to metallic surfaces, ladle rims, or various furnace areas.
Grippers, molds, and other tools can also be coated in a simple manner.
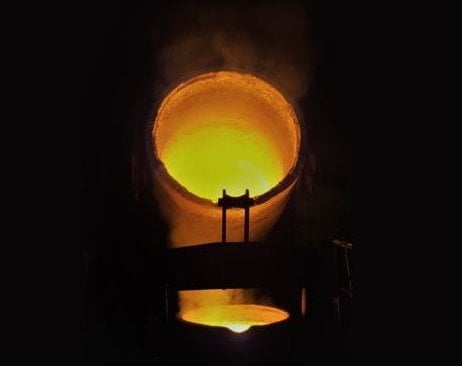
Zircon-Free Coating Technology
Our formulations are designed to meet your specific casting conditions and metal types, offering a sustainable choice without compromising the essential properties required for great casting results.
Mold Lite Plus 8000 Series
is an alcohol-based, high–solids, zircon–free coating designed for large iron and steel castings. This product can be prepared with Reducer 990 to the application density. The product's robust formula allows it to work successfully in all application methods but excels in flow-coat and spray applications.
Dura Kote 8000 Series
is a water-based, high-solids, zircon-free coating designed for large iron and steel castings. Dura Kote offers an eco-friendly refractory solution characterized by low VOCs, low HAPs, and minimal odor. This coating has an option for a color change dry indicator. The product's robust formula allows it to work successfully in all application methods, but it excels in spray and flow-coat applications.
Learn about Refractory Coatings
A good refractory coating can bring significant value to your operation through improved surface finish or reduced cleaning costs. Refractory coatings are a complex mixture of ingredients in which each plays a part in the final product's application characteristics, stability, surface finish, resistance to cast defects, and cost. Be sure to contact your HAI sales representative to determine which coating best fits your foundry's needs.
To learn more about refractory coatings, download our complete Refractory Coating Brochure.
Your contact
Daniel Cygal
Product Manager Coatings
.png?width=350&height=350&name=Untitled%20design%20(35).png)