Premium No-Bake Molding Solutions for Efficient Foundry Operations
Synthetic resins have been used since the early 1960s to produce molds and cores for large and one-off castings. HA was one of the pioneers in the field of synthetic resins. The introduction of furan resins in foundries and the development of No-Bake phenolic resins set important milestones.
Our No-Bake resin systems are continuously optimized through intensive research and development to meet the steadily increasing requirements of foundries and their customers over the past decades.
The No-Bake resin systems are used in the production of small, large, and very large molds. They are characterized by being optimally adapted to the requirements of the castings and the foundry's production processes.
The flexibility of the systems is also the reason why modified No-Bake resins are used on most 3D printers worldwide. This is ensured not only by the uncomplicated processing but also by the high storage stability of molds and cores.
No-Bake resins - our contribution to the energy transition
Especially in the production of large castings - such as rotor hubs for wind turbines - our binders are indispensable. The required cores and molds could not be produced without high-quality resin systems.What makes our resin systems so special?
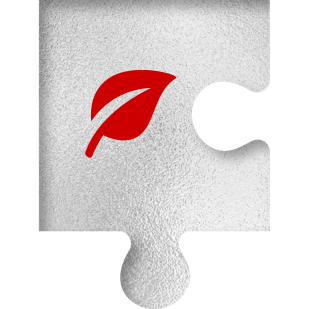
Significantly reduced emissions
e.g. through HA's industry leading TEOS systems
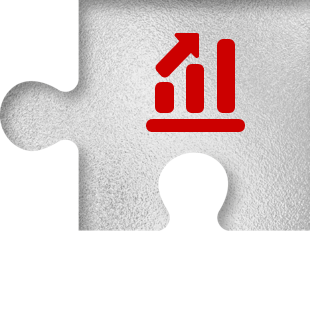
High productivity
Controllable processes, low defect tendency, excellent casting results
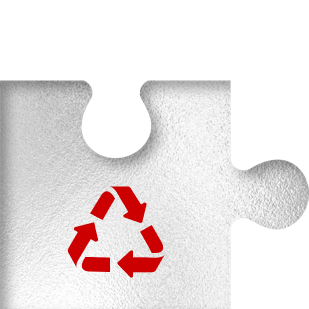
Sand Reclamation
All sands using HA's No-Bake systems can be reclaimed and reused
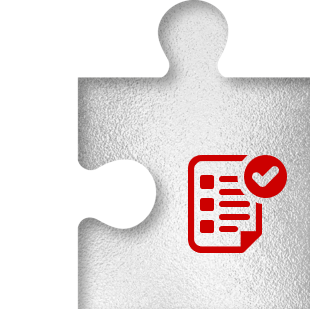
Compliance with environmental regulations
Least smoke and odor, providing the cleanest foundry environment
Our No-Bake product portfolio
Furan resin
This classical all-purpose method is used for the production of nearly all types of casting features
What its special features are:
- Low resin addition level
- Low viscosity
- Long storage life
- Good through curing
- Low odor
- Low emissions
- Easily recoverable used sand
- Nitrogen-free grades of resins that are particularly suitable for high-quality steel castings
- Reactive, rapidly curing specialty resins offering short stripping times
- Low-sulphur systems for high-quality ductile iron, a marked decrease in SO2 emissions during and after pour-off
Phenolic No-Bake (PNB)
The advantages of our phenolic No-Bake resin product portfolio:- Low-nitrogen resins
- Long sand work time
- Low over-cure tendency
- Uniform curing
- Reduced emissions during curing
- Easily recoverable used sand
Polyurethane No-Bake (PUNB)
Reactive system for short and medium series. Special features:
- Even more environmentally friendly due to improved solvents
- Short curing times despite a relatively lengthy sand bench life
- Low binder addition levels
- Unsurpassed sand flow
- Smooth, firm moldings
- Good separation from core boxes
- Low odor profile
- Free of sulfur and phosphorous
- Good surfaces in steel casting, free of cracks
- Low tendency for heat cracking
Alkaline Phenolic process
This method is used for high-quality steel castings, in particular steel castings, with the following properties:
- Very good casting surfaces
- Considerable reduction of finishing costs
- Free of nitrogen, sulfur, and phosphorous
- Patterns are easiliy stripped
- Low emissions during curing and pour-off
- Low carbon uptake in steel casting
- Low tendency for heat cracking and finning
- Good shake-out properties
Your contact
Aaron Kaboff
Product Manager Resins
.png?width=350&height=350&name=Untitled%20design%20(45).png)