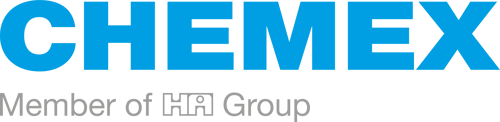
Innovative Feeder Technology
Our subsidiary, Chemex Foundry Solutions GmbH—Chemex for short—supplies customers around the world with a wide range of state-of-the-art feeder systems. Founded in 1974, Chemex has become a global technology leader in feeder systems.
The Chemex team is dedicated to collaborating closely with customers to optimize their castings through precisely matched feeder systems, increase output, minimize separation and fettling/cleaning costs, and are constantly in development to improve efficiencies in recipes and feeder geometries.
A strong team of product managers is on hand at all times to provide optimal service for customers, including expert advice on the company’s standard portfolio and the development of tailor-made solutions.
The strengths of Chemex feeders
Research and development in alliance with HA
Chemex is already a global leader in the field of feeder technology. Nevertheless, the company never rests on its laurels or stops researching and developing new products. As a member of the HA Group, Chemex has access to the extensive expertise of one of the world’s leading foundry chemistry suppliers. With the aim of offering customers even better solutions, the company’s research and development team is constantly working on and testing new materials and approving them for series production.
Patented
Sands, insulating materials, exothermic components: every year, 10,000 tons of raw materials are processed in Delligsen, where it all began. Since then, Chemex manufacturing has continued to grow, with manufacturing now in the United States. Each product variant has its own recipe, according to which the feeder mass is precisely mixed to the very last gram. The compositions – some of which are patented – constitute Chemex’s expertise. The specific material formulations determine the eventual insulating and exothermic properties.
Consulting at the highest level
Chemex is justifiably proud of its close collaboration with its customers. In North America, HAI has a team of 4 foundry engineers who put their knowledge and experience into practice to optimize the feeding technology and the cost structure of the individual castings on site together with their customers. Behind the dedicated resources in the United States for Chemex is HAI’s Sales and Technical Services, which will coordinate and work with all of HA Group’s resources to find the proper solution.
Sometimes very small, sometimes very big
Based on individual calculations, feeders are specifically designed for each application. The extraordinary variety of products supplied by Chemex gives customers the perfect choice for their specific applications. The spectrum of feeders ranges from the very small to the very largest, with volumes of over 3 gallons (11 liters).
Sustainable use of resources
HAI is certified according to the environmental management standard ISO 9001:2015, so the company’s responsible and sustainable use of resources is well-documented. Our first core shooter in the United States was installed in 2021. Here in the US, we follow our German standards and our own EcoMission. The company’s careful stewardship, mindfulness of the available raw materials, and constant monitoring and improvement of ways to use resources are constantly monitored and improved.
Tested and certified quality
HAI works with a quality management system according to ISO 9001:2015. The quality of the company’s feeders is tested using a range of methods, including thermo-physical testing. Parameters such as gas permeability and bending strength are also systematically monitored. Ignition and burning times are determined in an exothermic test.
The Chemex Mobile App
With this application for your smartphone or tablet, you benefit from many advantages. On the one hand, the product finder enables you to quickly and easily find the right product depending on your molding process and the alloy to be cast.
As an innovative partner, Chemex would like to support you in your everyday routine by providing this service in the best possible way. This is another step towards the digital future. If you have any questions regarding use or suggestions, please contact your responsible product manager or write to us at Brodie.Biersner@HA-Group.com
Side-Insert-Sleeve
The Side-Insert Sleeve is one of Chemex Foundry Solutions GmbH's latest developments. It was developed mainly for customers using vertically partitioned molding lines. This one-piece feeding system's biggest advantage is its easy and automatable positioning in the mold face with the help of the core inserter.
In addition to the air removal via the feeder at the partition level, the system also achieves an increase in output. In many cases, this increases the efficiency of pattern plate layouts.
Tele-Side Riser
With the Tele-Side Riser system, Chemex has made its innovative, proprietary telescopic technology available for vertical molding lines. It includes all of the advantages of our classic Tele-Feeder System, such as high-volume output and low fettling effort, thanks to its minimal footprint.
As with our Side-Insert Sleeve, air can be discharged via the mold partition. The system’s improved output allows more or larger castings to be placed on the pattern plate.
Tele-Feeder
The two-part Tele-Feeder System is a Chemex invention and also our flagship feeding solution. The greatest advantage of this system is its innovative telescopic technology, in which the upper section slides over the lower section during the molding process.
This guarantees enhanced compaction of the molding sand below the feeder while allowing the system to absorb much of the energy of the compaction pressure. The lower section is thus protected from the compaction pressure, thereby creating a defined break-off point, which minimizes releasing and cleaning costs.
Tele-Shell Feeder (Tele-SF System)
The Tele-Shell Feeder from Chemex combines the advantages of the Tele-Feeder System with those of a classic spherical feeder. The thermodynamically favorable spherical shape creates an optimal ratio between volume and surface area.
In combination with a short feeder neck, significantly lower riser heights can be generated compared to the traditional Tele-Feeder System. The Tele SF is, therefore, particularly suitable for use on molding lines with low cope heights.
.png)
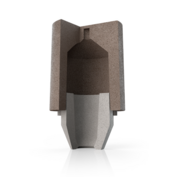
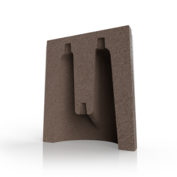
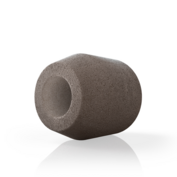
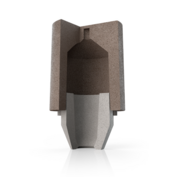
.png)
.png?width=350&height=350&name=Untitled%20design%20(37).png)
Your contact
Brodie Biersner
Senior Product Manager Feeders